BMW Group se centra en la digitalización
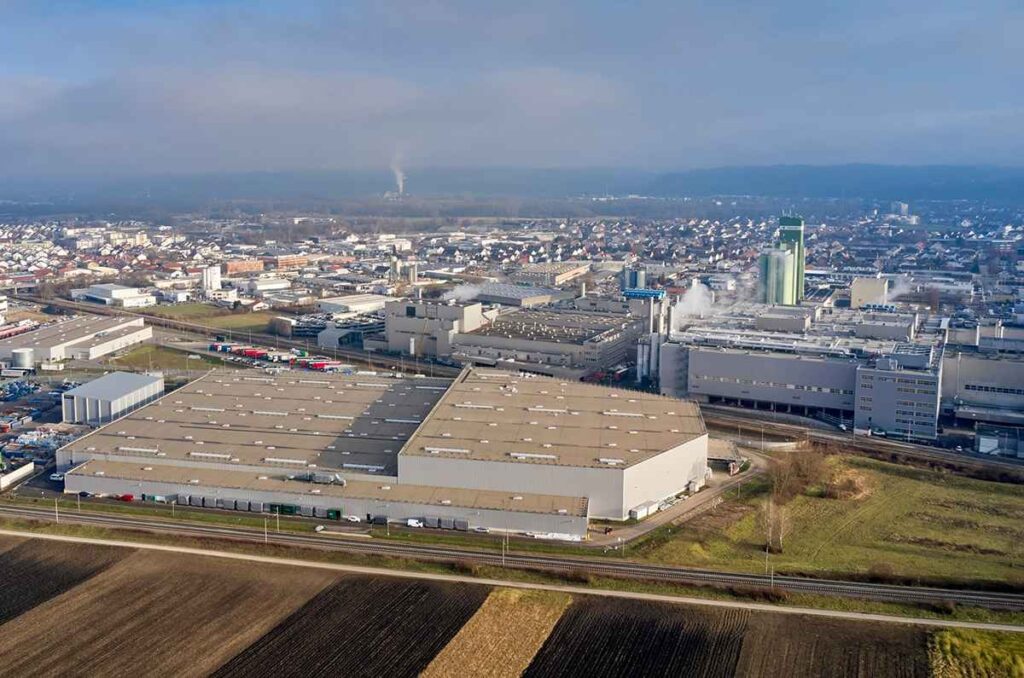
Detrás de cada coche digital también debe haber una fábrica digital BMW Group está mejorando de manera constante la digitalización en la producción de sus […]
Detrás de cada coche digital también debe haber una fábrica digital
BMW Group está mejorando de manera constante la digitalización en la producción de sus componentes. Desde la gestión de producción impulsada por IA y procesos logísticos inteligentes hasta controles de calidad basados en datos, la Planta de Landshut, el mayor sitio de fabricación de componentes de la empresa, utiliza tecnologías de vanguardia y, por lo tanto, desempeña un papel central como centro de innovación dentro de las industrias automotriz y de proveedores.
En la Planta de BMW Group en Landshut, por ejemplo, la empresa utiliza análisis de datos apoyados por IA para detectar anomalías en el tráfico de datos en una etapa temprana y prevenir ciberataques. Además, se utilizan el control de procesos digital y las instalaciones de producción en red para aumentar la productividad y mejorar la calidad.
Este video te puede interesar
Thomas Thym, Jefe de la Planta de BMW Group en Landshut: “No solo implementamos el progreso técnico, sino que también lo moldeamos activamente para asegurar nuestra competitividad a largo plazo. Detrás de cada coche digital también debe haber una fábrica digital.”
Shopfloor Digital en la Fabricación de Componentes: Producción Conectada para Mayor Transparencia
Un componente clave de la estrategia de digitalización de BMW Group es el programa de transformación “Shopfloor.Digital”. El objetivo es armonizar los procesos de fabricación y los sistemas de TI a nivel mundial en todos los 30 sitios de producción. Para lograr esto, la empresa está construyendo una arquitectura de TI moderna basada en la nube y confiando en la automatización de procesos y soluciones de IA. Como sitio de fabricación de componentes, la planta de Landshut es un componente clave de este programa de transformación. “Vemos la complejidad como una oportunidad y utilizamos los datos que obtenemos para mejorar continuamente nuestros procesos”, explica Franz Heigl, Jefe de Digitalización de la Fabricación de Componentes.
Gestión Esbelta: Herramientas Digitales para Procesos de manufactura esbelta.
Al mismo tiempo, BMW Group está impulsando la digitalización de sus enfoques de gestión lean. Esto incluye un mapa de procesos digital en las áreas de producción, un proceso de interrupción digital y gestión de flujo de valor. Para asegurar la alineación común de la organización, el proceso de desarrollo de objetivos sirve como una herramienta efectiva de liderazgo y dirección, permitiendo que los objetivos se desglosen en sus fundamentos y se traduzcan en desafíos concretos. “Nuestro objetivo es centrarnos en lo esencial en nuestro negocio diario y priorizar las actividades que crean valor”, dice Heigl.
Producción inteligente, logística inteligente: Cadenas de suministro y producción conectadas para mayor flexibilidad y eficiencia
BMW Group también está persiguiendo de manera constante su iniciativa de digitalización en logística y fabricación. Con la ayuda de sensores, datos en tiempo real y procesos impulsados por IA, la Planta de Landshut está optimizando sus cadenas de suministro, flujos de material y procesos de producción. Esto permitirá que los sitios de producción estén aún más conectados con los proveedores para evitar cuellos de botella y conservar recursos.
Un ejemplo de esto es la producción del BMW Energy Master, la unidad de control central de la batería de alta tensión para los vehículos de la Neue Klasse. Un monitoreo integral en línea, incluidos sistemas de cámara basados en IA, así como pruebas de sistema 100% al final de la línea en un entorno de sala limpia, cumplen con los más altos estándares de calidad. La Planta de Landshut suministrará en el futuro a todas las plantas de ensamblaje de baterías en todo el mundo con el BMW Energy Master, donde la unidad de control se montará en la batería de alta tensión en un paso final de ensamblaje.
La Planta de Landshut también confía en la automatización y digitalización en la producción de cockpits. Durante el control de calidad final, se verifican alrededor de 50 características de calidad en solo 30 segundos. Esto es seguido por el embalaje y transporte totalmente automatizados de las piezas. Esto implica sistemas de transporte autónomos que se mueven de manera independiente desde el punto de partida hasta el destino sin depender de un sistema de control externo.
En la fundición de metales ligeros de la planta de Landshut, BMW Group está produciendo actualmente carcasas de aluminio para los motores eléctricos de la Neue Klasse en una producción en pre-serie. Se aplican altos estándares de calidad en la fabricación de nuestros productos. Para garantizar que estos estándares se cumplan de manera consistente, se utilizan tecnologías modernas, como la tomografía computarizada (CT) en línea. Cada carcasa de motor eléctrico fabricada en la Planta pasa por un escaneo CT totalmente automatizado. En solo 42 segundos, se capturan 2,400 imágenes individuales y se reconstruyen en un modelo 3D del componente. A diferencia de la mayoría de las aplicaciones en el campo médico, el control de calidad aquí está completamente automatizado utilizando inteligencia artificial. Esto permite que la potente tecnología CT se integre de manera extremadamente eficiente en el proceso de producción, al mismo tiempo que se asegura la calidad de las piezas.
Calidad en la Cadena de Suministro: Calificación de Proveedores
Para garantizar altos estándares de calidad en la producción, BMW Group también se está enfocando en la digitalización en su cadena de suministro. En el Campus ZDSC (Cadenas de Suministro Sin Defectos), los proveedores reciben capacitación interactiva sobre temas como la gestión en el taller, sistemas de producción y digitalización. El objetivo es trabajar con los socios para establecer un sistema de producción estable con una “mentalidad de cero defectos”. De esta manera, BMW Group involucra activamente a sus socios y proveedores en la transformación digital.
AI Lab
El AI Lab es un nuevo espacio de innovación y colaboración que permite a todos los empleados de la planta de Landshut del BMW Group probar y aprender nuevas tecnologías basadas en IA utilizando ejemplos orientados a la aplicación. Los ejemplos de aplicación cubren un amplio espectro de aplicaciones de IA: el Radar de Tendencias Tecnológicas proporciona una visión estructurada de las aplicaciones de IA directas e indirectas, clasificadas por tecnología y nivel de madurez. Con PowerApps, los empleados pueden crear sus propias aplicaciones digitales sin necesidad de conocimientos de programación, digitalizando así procesos y automatizando tareas. El sistema informático AIQX (Inteligencia Artificial Calidad Siguiente) permite la automatización y optimización de la garantía de calidad en la producción utilizando IA.
Los días 14 y 15 de mayo de 2025, la planta de Landshut presentó su producción de componentes ya implementada, interconectada y basada en datos en el “Día de la Fábrica Inteligente”.